MOLLE (Modular Lightweight Load-carrying Equipment).
The Molle System features a modular attachment system. This system uses a ladder-shaped design called PALS. PALS consists of rows of heavy industrial-grade nylon. It sews onto the vest for more attachments and accessories. This system has become the standard for modular tactical equipment. It replaces the Universal Lightweight Personal Carrying Equipment (ALICE) system. The ALICE system was used in the earliest modular vest systems.
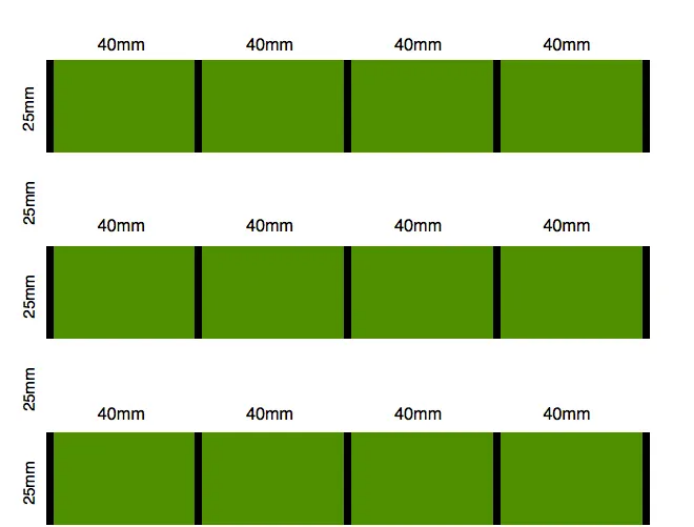
The principle of MOLLE is straightforward: it involves the horizontal and vertical interweaving of webbing. Most of the PALS webbing of the main carrying equipment is arranged horizontally. The active longitudinal webbing interlaces between the horizontal webbing on the accessory bag and the horizontal webbing on the carrying equipment. Finally, it is fixed by snaps to achieve a stable addition of carrying modules.
Traditional webbing VS Laser cutting
The initial form of MOLLE is to sew 1-inch wide ladder-shaped nylon webbing on nylon cloth every 1 inch to form a grid-like mounting system.
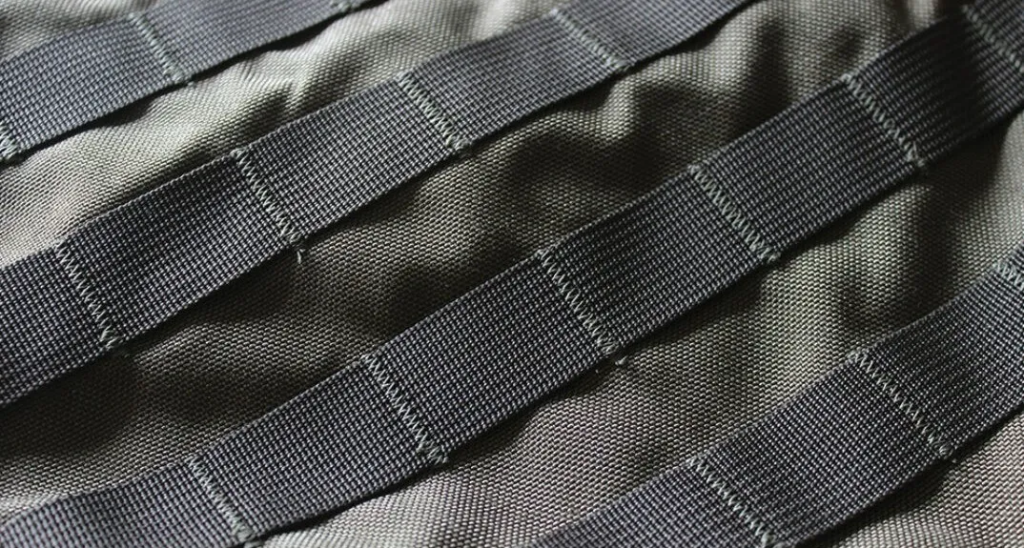
Later, with the development of textile technology and new materials, laser cutting MOLLE appeared, and the use of machines to cut MOLLE-sized holes on specific fabrics was undoubtedly a revolutionary progress in the productivity of tactical equipment.
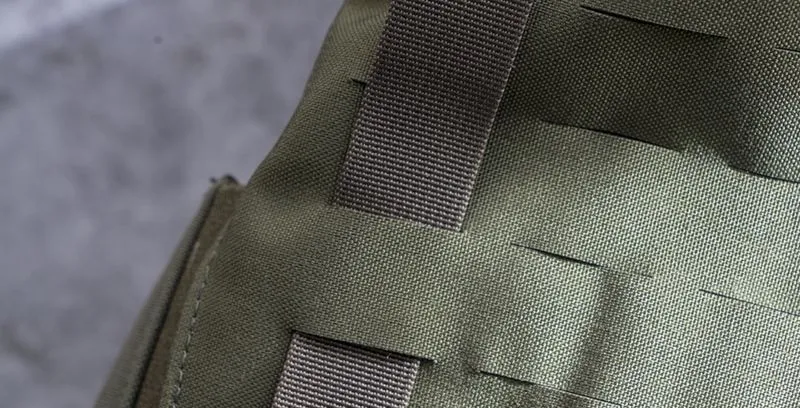
Compared with traditional webbing, optical cut MOLLE has the following advantages:
①Higher overall strength
The stress point of traditional webbing is mainly at the seam, and its strength is affected by multiple factors such as webbing, seam and base fabric. When optical cut fabric is pulled, the fabric around the stress point can disperse the stress, so the strength is higher.
②More flexible equipment adjustment
When using the optical cut MOLLE carrying platform, when adjusting the height of the equipment, it can be adjusted in units of 1 inch (25mm). In order to achieve this effect with traditional MOLLE, a row of sewn webbing is required, which is ugly and increases the weight.
③Better anti-hooking effect
After all, the sewn webbing at the bottom is convex, while the optical cut MOLLE is flatter and has an inherent advantage in preventing hooking.
④Cooler and more beautiful
This is purely the author’s subjective opinion. Some comrades prefer traditional webbing. This kind of thing is different for everyone.